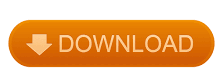
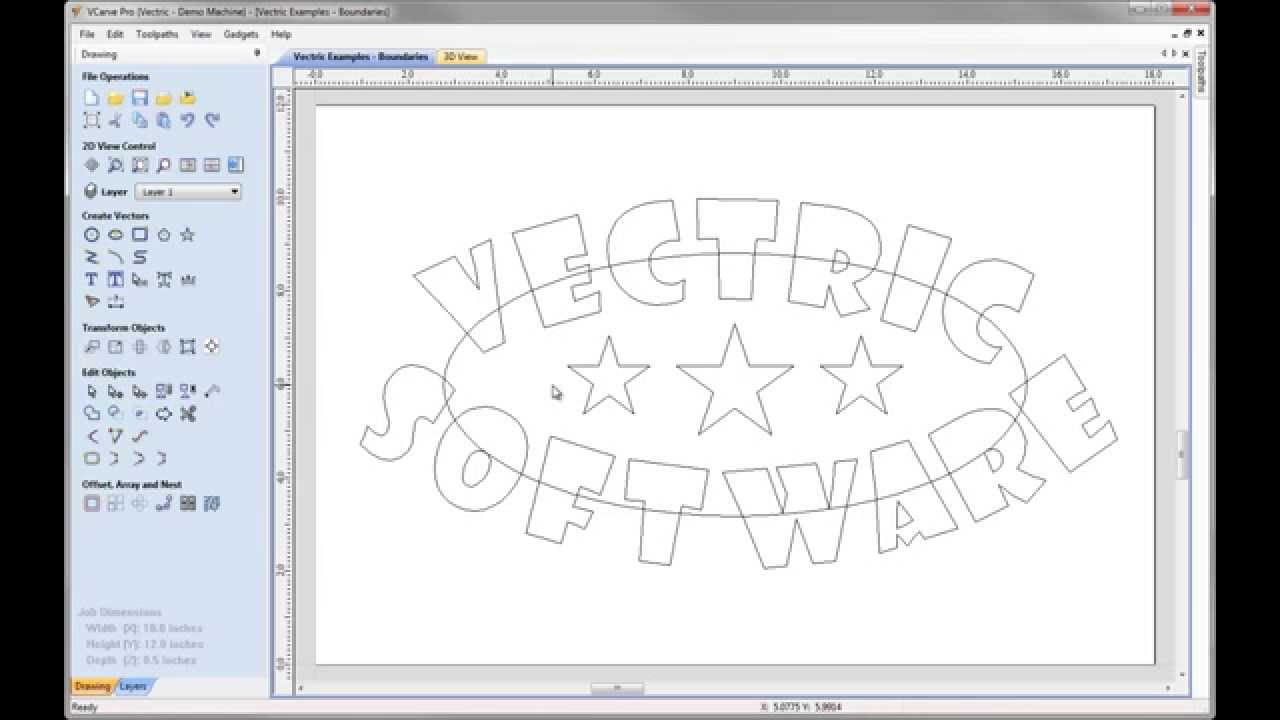
Visual Example, Kress spindle with double 5mm spacers So you would subtract another 2-3mm from the above numbers in a practical application.

If you use an engraving blank that sticks out say 12mm from the bottom of the collet nut, then that means you can have a max material height of 101.66mm (4″). NOTE: This would also mean that the cutting height of the tool would have to be a min of 56.83mm (2.23″) or you run the risk of rubbing the shank of the tool on the material.Įxample 2: If you intend to only engrave on top of a piece of material, then your tool stick out can be much less.If you want to cut all the way through material, you would need to have a tool that is long enough, which you would further subtract from the new Z height value.Įxample 1: New Z Value is 113.66mm (4.47″), if you divide that number in half, that would mean you can use a piece of material that is 56.83mm (2.23″) thick and the tool would have to stick out 56.83mm (2.23″) as well. Now depending on what you intend to do, you can use this new value to plan your project. So if you take into consideration the MM-1000 with dual spacers, you would have a total Z height of 140mm (5.51″) minus 26.34mm (1.04″) leaving you with a new max Z height of 113.66mm (4.47″). Most all CNC machines will have spindle and spindle nut/tool holder stick out that takes away from the usable Z height. NOTE: This is the case with just about every CNC machine on the market, not just STEPCRAFT CNC.The following represents the spindle and spindle nut stick out you get on a D-Series machine with the HF-500 and MM-1000 spindles From this height you need to subtract the spindle collet nut stick out as well as the length of the cutting tool you are using. However this does not represent the maximum height of material you can process. The D-Series 420, 600 and 840 all have a max Z height of 140mm (5.51″). What is the total usable Z height on the D-Series CNC? Consult your machine’s manufacturer for assistance with proper speeds and feeds for surfacing bits. Note: Because of the larger diameter of a surfacing bit, it is important to note that you can not take as deep of passes or run as fast as you might with smaller end mills on most machines. By using a surfacing bit, you will ensure that your spoil board is perfectly level in relation to your gantry which will result in a uniform engraving. 005″ into a piece of metal and your bed is off by a couple thousandths from one side to the other or front to back, then the thickness of your engraved lines will vary. Leveling your spoil board is also important.
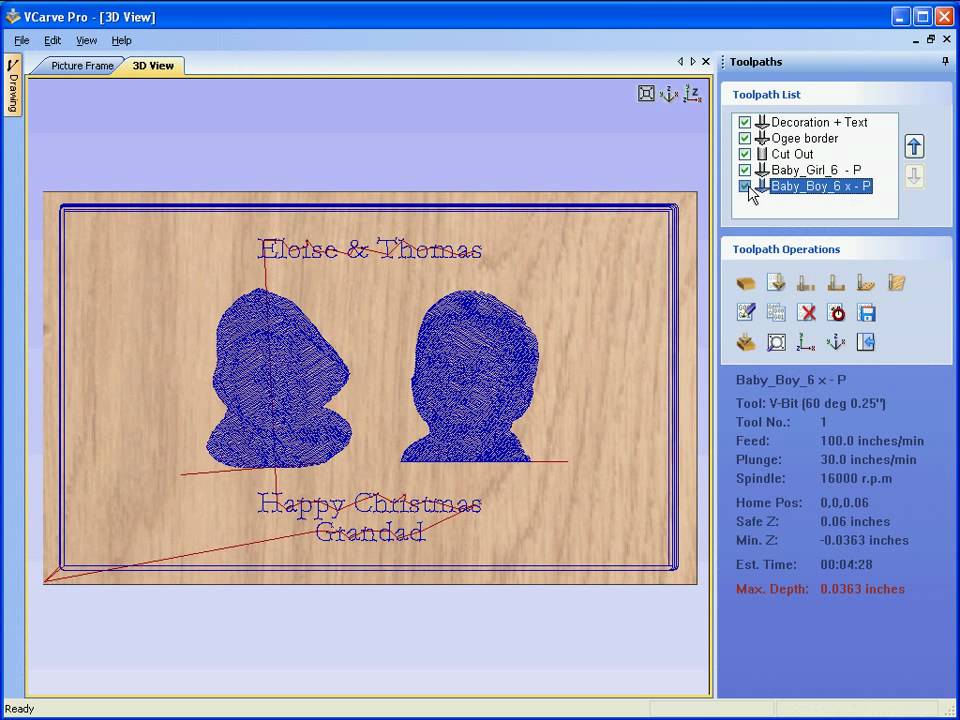
A surfacing bit is perfect for this, especially with machines where the spoil board is physically attached to the machine – you might want to prolong the use of it for as long as you can before replacing. After continuous use your spoil board’s surface will have a lot of cuts in it and you might want to clean it up so it is perfectly smooth again. If you don’t have a surface planer in your shop then you can use a surfacing bit with a pocket tool path to plane the material down.Īnother common use for surfacing bits is to clean up and level a spoil board. For example, you might have a piece of rough cut lumber that measures 1 inch in thickness but you need it to be 3/4 inch thick. They are also used to take the thickness of a material down to a final required size.
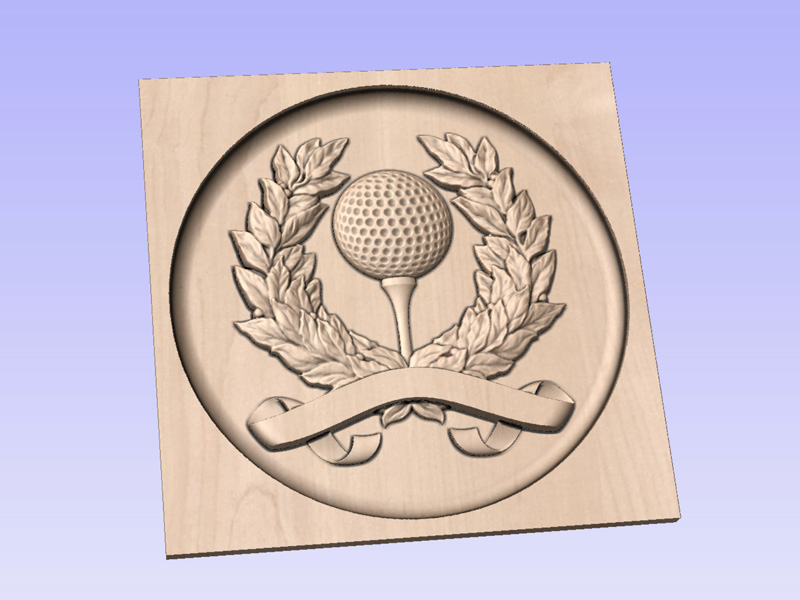
A surfacing bit typically has a larger than normal cutting diameter (1 to 3 inches) and are used to flatten or level uneven surfaces on your project material.
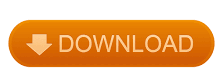